The Importance of Quality Materials in Cement Production
- Brandcodax
- Apr 21
- 4 min read
Cement production plays a vital role in the construction industry, serving as a fundamental building material. The quality of cement significantly impacts the durability and strength of structures. Central to producing high-quality cement is the selection of quality materials, which can enhance performance and reduce environmental impact. In this post, we’ll explore why using superior materials is crucial in the cement production process.
Understanding Cement Production
Cement production is a complex process involving various stages, from raw material extraction to the final grinding of the product. The primary materials used in cement manufacturing are limestone, clay, and other minerals. However, the introduction of high-quality additives greatly improves the performance and sustainability of the final product.
For instance, incorporating pozzolanic materials, like volcanic ash or fly ash, alongside traditional materials can lower energy consumption during production and increase the concrete's durability. This combination not only improves the quality of the cement but also addresses rising environmental concerns surrounding traditional cement manufacturing processes.

The demand for quality in cement production has risen significantly. This is largely due to increased stringent building standards and regulations that ensure structures provide enhanced safety and longevity. When manufacturers prioritize quality materials, they are better positioned to meet these standards.
Factors Affecting Cement Quality
Quality in cement production is determined by several factors, including raw material selection, chemical composition, and the manufacturing processes employed. Let's break down these factors:
1. Raw Material Quality
The core ingredients of cement include limestone, clay, and iron ore. However, the purity of these materials is essential. For example, impurities in limestone can lead to defects in the final product. High-purity limestone typically contains greater amounts of calcium carbonate, which is necessary for the formation of clinker in the kiln.
Moreover, clay should contain appropriate silica, alumina, and iron compounds. The right balance ensures effective reactions during the production process. Using substandard raw materials can adversely affect the physical and chemical properties of cement, leading to inferior quality.
2. Chemical Composition
The chemical makeup of the raw materials directly impacts the characteristics of the cement. Ideal ratios of lime, silica, alumina, and iron oxide create a successful blend for efficient clinker formation. For instance, having a higher percentage of lime can lead to better strength attributes in the final product.
To ensure that the chemical balance remains within specified limits, manufacturers often conduct regular testing of raw materials. This involves assessing the physical properties and chemical composition before, during, and after the production process.

3. Manufacturing Process
The production process involves several stages, including crushing, raw milling, and clinkerization. Each stage needs careful monitoring to maintain high-quality output. If one step is compromised, it can lead to a decline in the overall quality of the cement produced.
For example, the temperature and duration of the clinkerization stage play pivotal roles. Insufficient heat can result in poorly formed clinker, while excessive heat can lead to over-burning, impacting the final cement properties.
How much coal is required for 1 ton of cement?
Coal is an essential fuel in the cement manufacturing process, providing the necessary energy for clinker production. Typically, around 450 kg of coal is needed to produce one ton of cement. This requirement may vary, depending on the efficiency of the plant and the technology employed in the cement production process.
Using high-quality coal for cement industry operations can lead to improved energy efficiency and lower emissions. High-calorific value coal provides more energy per kilogram, which can reduce overall fuel consumption, minimizing the carbon footprint of cement production.
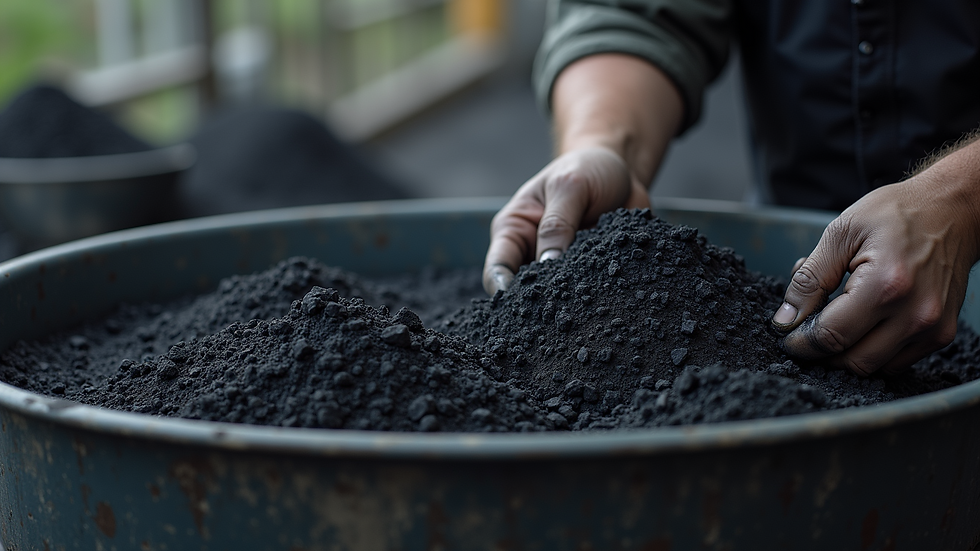
The move towards using alternative fuels and resources in the cement production process is gaining popularity. Many manufacturers are integrating waste-derived fuels and renewables to reduce reliance on traditional fossil fuels like coal, which helps in minimizing environmental impact.
Advantages of Using Quality Materials
Investing in quality materials during cement production has several advantages:
1. Enhanced Durability
Cement made from high-quality materials generally exhibits greater durability and resistance to environmental factors such as exposure to moisture, chemicals, and extreme temperature shifts. This is particularly vital in construction projects that are expected to last for decades.
2. Improved Workability
The use of superior raw materials results in improved workability of cement. This means that the cement can easily be mixed, poured, and shaped during construction. Enhanced workability leads to better finish and aesthetics.
3. Cost-Effectiveness
Although there may be an initial investment required for high-quality materials, the long-term savings often justify the expense. Buildings made with quality cement require less maintenance and repair, ultimately saving on costs for homeowners and contractors alike.

4. Environmental Sustainability
Quality materials often contribute to more sustainable cement production practices. By extending the life cycle of buildings and reducing the need for repairs, using high-quality materials supports environmental goals. The cement industry is under pressure to lower its emissions and reduce waste, so choosing better materials aligns with these objectives.
Innovations in Cement Production Materials
The cement industry is continually evolving, with innovations that push the boundaries of quality materials. Some trends to note include:
1. Sustainable Additives
The integration of sustainable additives, such as polymeric resins and biopolymers, can enhance the properties of cement while lowering harmful emissions. These additives improve the environmental impact of cement production and offer significant benefits during construction.
2. Recycled Materials
Many manufacturers are now turning to recycled materials, such as ground granulated blast-furnace slag (GGBS) and fly ash, to supplement traditional raw materials. These substitutes make use of waste products from other industries, contributing to a circular economy and minimizing landfill waste.
3. Digital Technologies
The use of digital technologies in monitoring and controlling raw material quality has made significant strides. Advanced analytics enable real-time assessments, improving the ability to react to quality issues promptly. This responsiveness has become essential in maintaining high-quality standards in cement production.
Building a Stronger Future
The quality of materials in cement production is a critical aspect of the construction industry. High-quality raw materials lead to a stronger, more durable, and more sustainable final product. As global construction demand continues to rise, the cement industry must adopt innovative strategies to ensure that quality standards are met.
Discussions around reducing environmental impact and enhancing the resilience of infrastructure are more relevant than ever. By investing in quality materials and advocating for sustainable practices, the cement industry can pave the way for a better future. Let's embrace these advancements to build structures that are not only strong but also environmentally responsible.